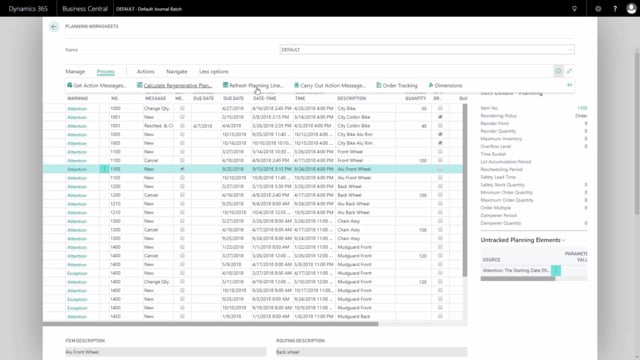
How to manually create production orders in Business Central?
In this video, I’m will show how to create a production order.
This is what happens in the video
Normally a production order could be created in two different ways, either manually or from the planning worksheet after calculating an MRP.
So first, I’ll show how to create the production order from the MRP plan.
If I go into the planning worksheet, and assume that somebody runned the plan.
And here I have the item that I’d like to process.
This is a production item, it says in the plan out here, production item.
And I can click accept action messages and then carry out action messages, and make sure that the production order is set to some action here, in this case, to create a firm planned production order.
This will create the production order and remove the line from planning worksheet.
And I can now find my firm planned production order in the firm planned production order list, and it’s down here.
So, I just made this production order automatically from the planning worksheet, and it was created by the calculation algorithm.
On this production order, which is now firm planned, I can enter my line and on the line, I can see the components, meaning the material requirements that are necessary for this order that I have to go and pick on inventory, and I can change it here manually if I want to, select some other items.
I can also on the line see my routing, if a routing is defined for the item.
A routing is the processes, I need to perform to make this order, and I can also change the routing here.
I can also from the process tab print job card and material acquisition that responds to the same two tables, meaning material acquisition is the list of the components, I need to go and pick on the inventory and this is typically a document for the warehouse employee.
And I can also print my job card, which is a document for the production people, and that will be one page for each operation.
So, in this case, I have 5 pages, because there are five different operations, one for each step in the process.
When I want to post on the production order, I need to release it first, so I need to change status, so the production order has different status, and now I would change status to Released, and we’ll transfer this firm planned production order to a new released production order.
So, now I made a released production order.
I could also have made the production order manually just by clicking New, either from the firm planned production order list, or the released production order list, and I choose the source type, item, and I select the number I’m going to produce, item number, and the amount, and from the process tab, I will select refresh and that will calculate the production order lines.
Here we are.
So, this is actually calculating the routing line and the component line that was shown before, and this is the same as the automatically calculated production order before, and again, I can change status in this one and release the production order, so it’s ready to actually go into production.
So, now I have made two different released production orders from firm planned orders, one manually, one from the worksheet, and if I enter my released production order list, I can see the two released production orders, and normally I would print the documents from the released production order.
That will be the most common to do.