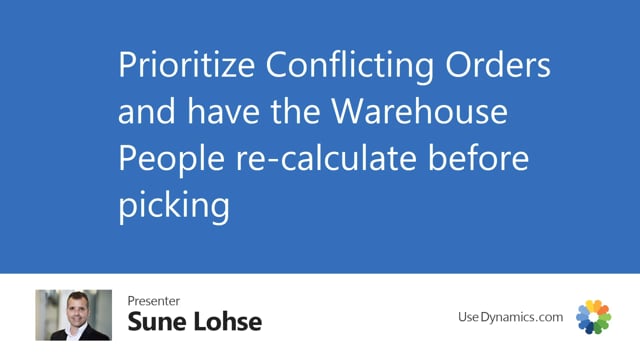
Once the warehouse people is done picking all the shortage orders with no conflict or with on stock, they should handle the conflict stock items and the sales responsible should somehow have prioritized this for the warehouse people to tell on which order they should take this sales orders.
This is what happens in the video
And then the first one of course will easily be able to ship, but when they take the next one and they enter the order, they should recalculate the shortage status.
And in my opinion, you should let the warehouse people do this directly if you’re not using shipping documents, etc, but only ship per order, then you could recalculate to make sure that the shortage status is still conflict stock, meaning you can still ship all this order. But once you ship this order and you continue to the next order, sometimes you will enter an order where it’s partial stock or no stock and you cannot ship it anymore.
So recalculate for each order or do a full recalculation each time you pick an order, but that might be a heavy job.