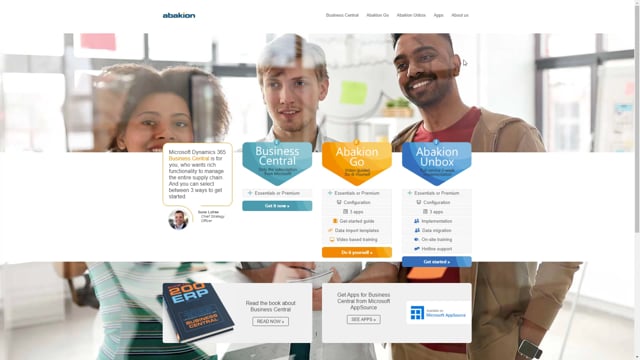
Let me try to run through the different shortage statuses on the sales order lines on the sales order header into the same field, and this is most easily explained on our landing page for the app. So let’s go to the landing page.
This is what happens in the video
So this is on abakion.com and we have our app landing page and somewhere in here, you could find the shortage on demand orders into that one.
And on this page, you’ll have a list explaining all the different shortage statuses here in the middle. Let’s try to look at that.
So the top one, the blank shortage status means that it’s actually not calculated.
On stock meaning that there’s enough items on stock to cover all demands within the period selected. Whereas conflict stocks means there’s enough item on stock to cover this specific line, but you don’t have enough to cover all demands for all items so starting to handle those orders will make conflicts or potentially make conflicts on other orders.
And when calculated, try to figure out if the first is possible. If not, then it goes to the next one. If not, then it goes to the next one, etc.
The next level is if you have an item with replenishment system production, then the complete production which means there are not enough items on stock to cover the demand on the lines and therefore, it calculates if we have components enough to produce this item to fulfill the supply on this order and all other orders with the same items.
Whereas the conflict production down here means that it’s possible to actually cover the lines on this demand by producing the items, but then other lines will not have so there’s a conflict on the component level, the lower levels so to say.
If this is not possible or the item is not a production item, it goes further and figure out do we have any stock at all? If we do have stock, it will be set as partial stock. If we don’t have any stock, it will calculate a partial production based on the component like on the conflict production and complete production and if it’s not possible to produce anything and there is no stock at all, it will be set to no stock or no production. So no production meaning you don’t have any stock on the items and you don’t have at least one of the components. Error meaning that it’s not possible to calculate. For example, if you have a production bill of material, which is not certified and you have no stocks so you try to calculate on the production level, but this will provide an error.