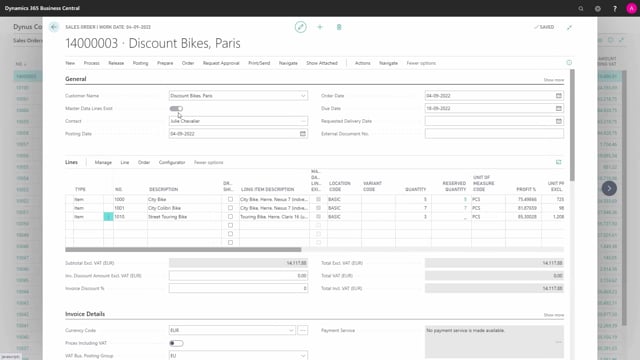
One of the ideas with this Sales Configurator is not to create a lot of master data.
This means you build on base items with bill of materials that are generically, then you enter a line with an item number like this on whatever quantities, and you search for an item that looks the most like the item the customer requires.
So, you have different base items, and then on the master data information on the customer requirements, you can change the parameters based on the customer demand, saying it should be another gear, another value here, another color, or whatever.
But this transfer down through the order hierarchy, and it’s transferred to the posted document, so it’s even possible to find it later on again, that you have produced this combination of master data.
And this is impact, of course, on this stuff we are producing or painting or whatever down the hierarchy.
But with a normal configurator where you create a new item each time, the system will be filled up with items that you only produce once, and bill of materials that you only use once.
And to avoid this, we prefer to do it this way.
So, it’s a more agile functionality, and it’s still possible to find the previous stuff based on history.
And of course, one of the paradigms here would be that the planner or whomever is configuring these changes the component list on the top level production order, and down through the hierarchy, all the changes that need to be made.
So, of course, the finished goods should take the correct components from stock or buy the correct components.