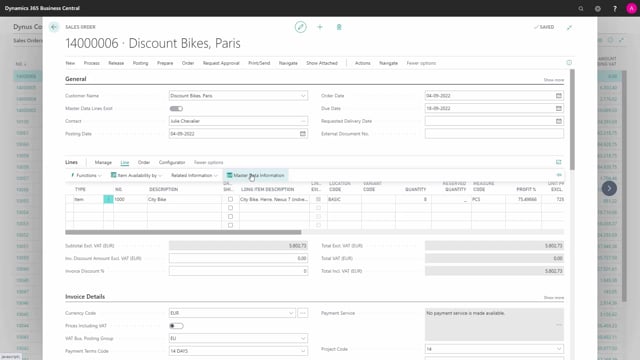
Once the salesperson has taken up the master data information from the customer, meaning the requirements that they would like to work with in production, and created a production order related to the sales order, a firm plan production order, but before creating the hierarchy, typically the salesperson will tell the planner or the item development responsible, who should go into this order and look at the item, look at the master data information, the requirement from the customer, and then correct the bill of material.
If it’s not, also correct it with the substitution functionality.
This means looking at the component list, figuring out if this is all the right component, and maybe also changing the routing, so it could be that some setup time will be much longer because it’s not a standard item anymore, and maybe also some of the run time will be longer.
In this way, prepare the production order and figure out if it’s actually possible, and after that, give feedback to the salesperson that it’s doable.