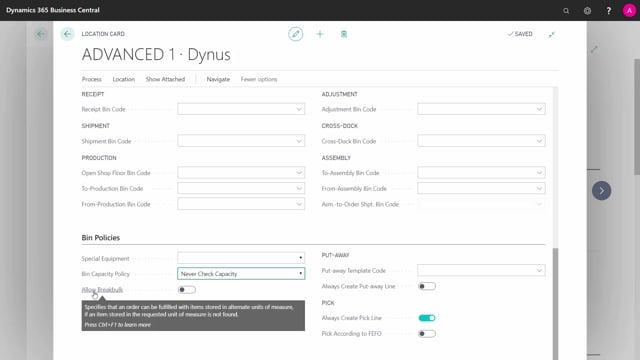
How to work with the fields in the Location Card in Business Central?
This is a walkthrough of the fields on the Location Card.
This is what happens in the video
Locations are the geographical places where we store our inventory, and you can define as many locations as you want to, I’ll show you the fields in the location card.
First, the unique key for the location and the name This checkmark is Use-as-in-transit.
It is meant for using this location for Transfer Orders, meaning when you ship the Transfer Order from one location, It has to be held somewhere in the system, until you receive it in the other location, so a transit location is like a buffer location.
The address on your location is self-explaining, and the contact could be a primary contact in charge of the specific location.
In the Warehouse tab, there are many selections.
One is Directed-Put-away-and-Pick.
If you checkmark it, all the others will be check-marked, and you can’t change them.
When you are using the full warehouse functionality, you are locked into using the functionality.
I’ll continue this demo with another location.
Let’s take my simple warehouse here.
We didn’t check the put-away-and-pick field, so we can select between all options here.
If we require to receive the goods and create a receipt document and do we require to create a shipment document on the outbound side.
Likewise, do we require to create a put away document, after receiving it on the ramp, would we like to use a document for putting away, so the warehouse guys can bring it around the inventory.
And is it mandatory to use a put-away worksheet? meaning that the put away document is not automatically created while posting the receipt, but is created in a worksheet.
You can only checkmark it if you have check marked the fields above, And the Require Receive field because those relate to those two.
Require Pick means you require on the outbound side to create pick documents, for picking the items before shipping it on the shipment.
The Bin Mandatory field means that you must enter Bin-codes every time you handle the item.
Use this, if you want to control items per bin, to have one item stored many places in your warehouse.
ADCS – Automatic Data Capture System is meant for automatic data capture and comes out of the box with Business Central, The market offers many other solutions for capturing data with scanner devices.
Default Bin Selection is stating whether you want a fixed bin to be the default bin, or you want to have the last used bin to be suggested by the system.
Outbound and inbound warehouse handling time is about the time calculated on the inbound and the outbound document, meaning, on a purchase order with an expected receipt date, and your inbound warehouse handling time is 2 days, entered as a date formula, the planned receipt date would be 2 days before, meaning, we expect the warehouse to use two days to handle the item before it’s available in stock.
So, this is a time buffer to make a slot for the warehouse people to get the item in or out of stock.
The base calendar code, you can select for the warehouse, is to calculate with days availability, and the customized calendar applies to your base calendar code, to make deviations, on specific dates we are not working, you can checkmark it here.
The Use Cross-Docking field can be selected if you use both shipments and put aways, you can cross-dock the item, meaning, instead of putting it into your warehouse, the item should be taken directly from the inbound ramp to the outbound ramp, so you don’t handle it in the warehouse, but can select it directly.
And the Cross-Dock Due Date Calculation is about how long time we want to look when checking for cross-docking items.
On the bin tab, there are many bin fields, you can use if you have check-marked the Bin Mandatory field.
What is your Receipt Bin Code? When you post the receipt on the inbound side, there’s a bin code for where the receipt should go, likewise on the outbound side What is the Shipment Bin Code? In the Production area, there’s an Open Shop Floor Bin Code It’s a general Shop Floor Bin, where you can put the item, then there’s a consumption bin, the To-Production Bin Code, if you pick from the warehouse for the production people to consume it, there’s a default bin code where you can place the item.
And when they output the item, they will put it on the From-Production Bin Code, where the warehouse people can pick it.
It’s the same on the assembly side, the two Assembly Bin Codes, and the Assembly-to-Order Shipment Bin Code is on the Sales Order, if you use Assembly-to-Order, you must have somewhere to pick your assembly item into a bin, the order can pick it from.
The Cross-Dock Bin Code is if you’re using cross-docking, and the Adjustment Bin Code is if you do inventory adjustments, there must be a bin code for positive and negative warehouse adjustments.
The Bin Policies apply to the checkmark with Directed Put Away and Pick, so we go back to the advanced location, The Bin Policy could be the Special Equipment code set to accord to the bin or to come from the item.
The Bin Capacity Policy is a maximum capacity in a bin.
Will you allow or prohibit to exceed the capacity.
Will you allow Breakbulk – to split from one Unit-of-Measure code to another, so if somebody wants to pick pieces, but we only store in boxes, do we allow the system to break a box for us? Put-away Template Code is used if you are using put-aways, you can define if you always want to create put away lines, even if there’s nothing to put away, should it create a line or not, likewise on the pick side, would you like always to create pick lines? Should it create a pick line, even though the item is not available in stock, and you may use this, if you expect the item to get on stock when you create the pick documents, and then a line should be there.
Normally, we suggest not to set this checkmark.
The field Pick According to FEFO, meaning First Expired First Out, If items have expiration dates, should the oldest item be picked first, or the one that expires first? These are the fields on the location card.