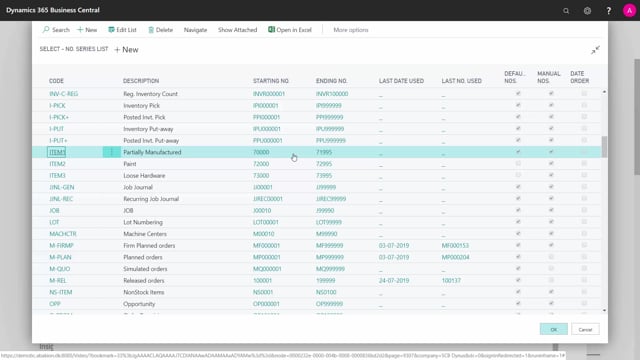
How to complete the inventory setup in Business Central?
Let’s look at the fields in the Inventory setup to explain what they are doing.
This is what happens in the video
The inventory setup determines how the inventory functionality works.
The first field on the General tab is the Automatic Cost Posting.
When you do postings, should the posting automatically go into the cost account, or would you like this to be done with the Post Inventory Costs G/L Batch Job.
Normally, you would set this one, so when you post the invoice or purchase order, the correlated Item Ledger Entry should be updated automatically, when you know the invoice.
Expected Cost Posting to G/L is when you want to post the expected cost …
again on a Purchase Invoice but all also other kinds of documents.
So when you receive Purchase Invoice, the quantity handling, and there’s an expected cost on the Purchase Line, should it create value entries for that? and then adjust or create the value entry when you post the invoice?
Or should it post the value entries when actually invoicing the Purchase Order?
And the argument for not setting this check-mark is, that it can be heavy postings.
And it’s more complex to read afterwards, if you’re looking into the entries.
Automatic Cost Adjustment is for when you do the cost posting or the cost posting batch job, would you like the system to post all the way back into the past?
Or would you like it only to post a day, a week, or a month?
Would you handle entries independent of the age of them?
Or will you handle entries only in a certain period.
Default Costing Method is applied when you create new items. This will apply on the Item Card.
And the Average Cost Calculation Type could either be per item in general.
So, it will just be the item determining it, or it could be per item, per location, per variant, meaning the SKU card.
So you will actually distinguish between the cost on different locations or variants.
Average Cost Period determines the period to calculate the average cost in, meaning, if you have very old open entries.
Would you like to include them when calculating the average cost, or in which period would you like to look back to calculate average cost?
Copy Comments Order to Shipment – and to Receipt – the two fields applies to Transfer Orders, meaning, when you post from a Transfer Order, should it transfer the comments to the posted documents, the receipt and the shipment.
The Outbound and Inbound Warehouse Handling Time is the default time …
it uses on inbound and outbound documents.
On the Location card, you can set it up as well.
So, you can distinguish per location what the in- and outbound handling time is.
And this is more likely default values.
It’s the time used in the warehouse to handle the order, so the planned receipt og shipment date will be different …
from the expected receipt or shipment date.
And thereby, the warehouse will get a slack of time …
to handle the item, when it’s not available.
If you check-mark the Prevent Negative Inventory, it’s not possible to post with negative inventory,
meaning, if it’s default not checked, you can sell an item that will provide a negative inventory,
and then put the item on inventory later on.
You don’t need the item in inventory before posting it.
It doesn’t apply to the Production functionality. You must have the item in inventory.
So, Production Orders always use Prevent Negative Inventory.
When you create a new item on a Sales Order, and the item doesn’t exist, the system will suggest you to create a new item number.
And if you don’t want suggestions, you can check-mark this field.
Then it won’t create new items from Sales Orders.
And with the Copy Item Description to Entries, you can select this if you …
want the item description to be transferred into the entries, when you do postings.
Location Mandatory is good to check-mark, if you’re using locations, because you shouldn’t post anything in location blank.
If you don’t check this, it’s possible to do postings both with Location Codes and without.
Normally, if you use locations, it’s suggested to check this one.
Item Group Dimension Code is a dimension, you can select from the dimension list, to do statistics or analytics on your items, and then you can have this default Dimension, and it applies to the analytics functionality in Business Central.
And at the end of the Inventory setup, you have all the default number series.
When you create new items, all these fields look into the numbers series setup, And here you will provide all number series, if they don’t come with your system.
And here, you can apply, when you create new Items, which number series should it follow, new Catalog Items, Transfer Orders, Shipments, Inventory put-aways, etc.
So these are all number series, that it follows, and you can change them here.