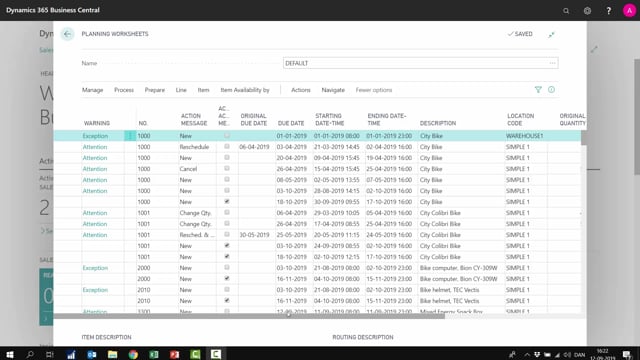
How to calculate items to purchase, to produce, to assembly, or to transfer in the same planning job in Business Central?
Calculating items to purchase, to produce, to assembly, or to transfer is done in the same batch job unless, of course, you manually set filters out of it when you select your items to plan. But if you run a complete MRP plan, they will be calculated at the same time. So this is a planning worksheet that I’ve just done, the one you see here.
This is what happens in the video
Calculated a complete plan, and if you scroll right, you can see that the first one is reference order type transfer meaning it was coming from a stock keeping unit card. Then I have an item with production order, I have purchase items, assembly items, and I’ll have production order again.
So here you can see that you can easily have purchase items on higher levels than other production order that depends on your hierarchy because it plans in low-level code order. So the reference order type would need to be mixed into the planning. So it would make sense just to do all production order planning first, then all purchase order planning, Etc.
So the only thing you could do separately, if it should make sense, is the purchase order planning. You could do that in the end because the purchase order has no components below and it has no effect on other items. So the purchase order could be planned in the end as a separate planning job.