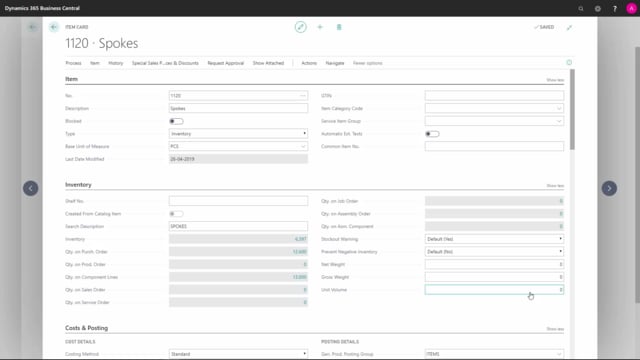
How to set up planning parameters on purchase items in Business Central?
As a purchaser working with Business Central, I can set up simple planning parameters on the item cards, if I want to use the requisition worksheet.
This is what happens in the video
In this video, we will show you what those simple parameters are and if you want to see more detailed parameters, you can look into the area of planning where we are more advanced.
But the simple parameter on an item card, and this is just an example for an item.
I need, of course, to fill in my replenishment on the replenishment tab that it’s a purchase order, I should fill in the lead time calculation, meaning the time it takes for me to get the item from the vendor, the vendor number and the vendor item number, if I have that.
That’s the simple replenishment parameters.
Then on my planning tab I should fill in my reorder quantity and if it is just a simple way of planning, you might use a fixed reorder quantity or lot-for-lot the reorder quantity uses minimum and maximum inventory, so after entering reorder quantity I should fill in the reorder parameters, meaning reorder point, reorder quantity, how many would I like to order and the safety stock level over here, would normally be filled in and then my order modifier, meaning my minimum quantity and order multiple, if I’m using that as well.
If I use lot-for -lot as a reordering policy, I should fill in at least my safety stock quantity down here, I would normally include inventory, not to ignore items already existing in the inventory, and I should fill in my lot accumulation period, which will be a date formula, for instance a month and also my rescheduling period which could be a month.
And the lot accumulation period is the period I would like to look across, when bundling demands together and the rescheduling period is the period I want to be able to change an existing purchase order.
After filling all of this on my item card, I’m ready to do requisition worksheet planning, meaning the MRP planning, from the requisition worksheet.