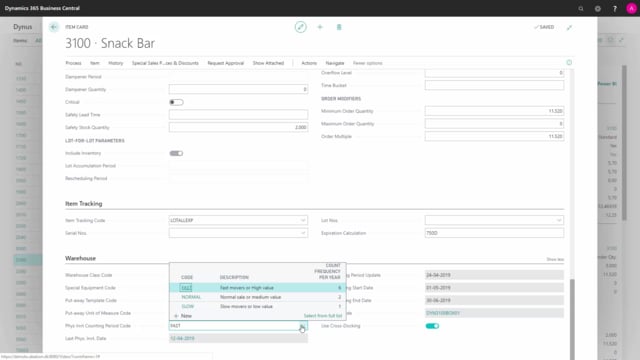
How do I work with advanced item fields in Business Central?
On the item card in Business Central we have some basic inventory fields explained in another video, that are relevant for the warehouse, and then we have some advanced inventory fields, meaning if you run advanced warehouse with bins and pics and put-aways, and then you can add a lot of information on the warehouse tab.
This is what happens in the video
The first one is the warehouse class code, where you can define a code for where to store this item in the warehouse, if it has specific needs for being dry or frozen, or whatever, you can define where to store it in the warehouse, as default you can define special equipment code if you need special equipment for handling this item, a special truck or a special gear or protection gear, you can define that in the table that you pick for the item here.
And then you can define a put-away template code, which put-away you would like to use for this item, when putting it into warehouse.
You can define, you can define a put-away unit of measure code, if that differs from the base unit of measure code or the purchase code, it’s possible to put it away in another unit of measure code, if the warehouse handle it differently.
Then you can define a physical inventory counting period code, which means how often would you like to count this item, when you create automatically suggestions for counting on the inventory, so you can define different values and define how frequent per year you would like to count this item.
And it relates to a function, where you can calculate those automatically.
And when you use that function, you update the last physical inventory date, which is the date you can drill down and see the last date, that this item has been calculated on the inventory, you can see the last counting update period, meaning what is the last time somebody ran this batch job, that calculated when to count the item, you can see the starting and the ending date of the next counting period, so it needs to be counted within that period some time, and you can see identifier codes, which are basically used with the ADCS functionality in Business Central, so normally we would suggest, instead of using those identifies here, to use the item cross reference list, item cross references with bar codes, you can set up but if you’re handling the ADCS, on the warehouse, this is the standard functionality of setting up unit of measures and per unit of measure per variant, you can define item identifiers, which makes it easy to scan on the inventory, the item directly per package or per item number.
And last of all, you have the used cross docking functionality, that you can checkmark, this basically means if you are allowed to cross dock this item, meaning if you have a demand on the outbound side, you can transfer it directly from the receipts zone, to the outbound zone, using cross docking, instead of putting it away on inventory and picking it again.
So, this is the fields relevant for the advanced field, relevant for warehouse employees.