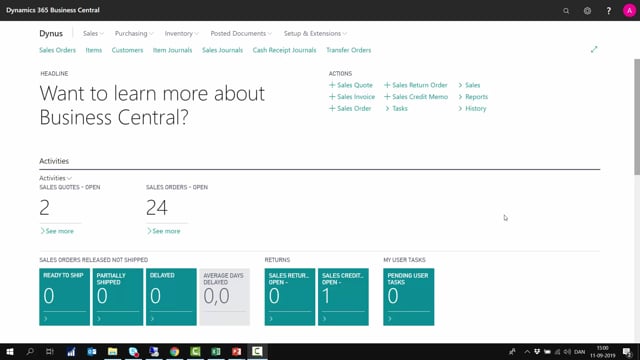
How to understand the difference between planning and replenishment in Business Central?
If you’re going to work as a planner in Business Central, it’s very important to understand the difference between planning and replenishment.
This is what happens in the video
And that means if you go into, for instance, the item card, it could also have been a stock keeping unit card and you scroll down to the areas of planning and replenishment.
Here we have replenishment.
Then we have planning and those are separated into two different areas.
And basically the replenishment is about how do I get my item when I plan the item and the planning this when do I need my item? So let’s see that in a small picture here.
So if the planning machine the MRP planning or the planning worksheet work as the little fellow in the middle. There was some input; meaning demands, supplies, inventory, master data, etcetera, and it does a lot of calculating and it comes out as output meaning all the proposals for production, orders, purchase orders and Transfer orders. So all this planning is in depending on the items replenishment system.
Meaning the date we need the item is in depending on the way we Supply it.
Let’s go back in Business Central and see what that means.
So this means when the planning is running, it looks at all the fields here on the planning tab, the reordering policy, Etc, figuring out by those parameters; planning per location, per variant, per item and figuring out what day do I need this item should be replenished and in what quantities, and when I’m done figuring out that, so this is the quantity, this is the date, it will look upon the replenishment tab and figuring out how do I replenish this item? Is that a production order? Then I use the routing to calculate the lead time, is that a transfer order.
If it’s on this queue card, then I use the transfer routings. If it’s a purchase item, I use the lead time down here to calculate the lead time. So the difference is that the planning runs first, it finishes, it gets the data in the quantity, and then it goes to the replenishment and figuring out how do we get it.