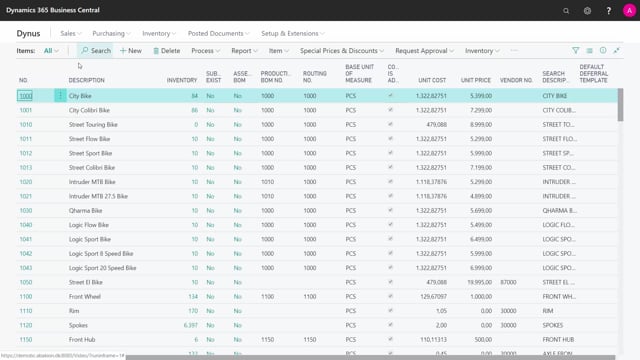
How to select a replenishment system for items or SKU's in Business Central?
Let’s see how you select replenishment system for items or SKUs in Business Central.
This is what happens in the video
Going into the item card, we have the tap replenishment system down here on replenishment and we have the replenishment system where you can select how to replenish this item.
This means when you have calculated the quantity you need at what date you need it, you need to define the replenishment system to figure out how you replenish it. You can select here from purchase, production order or assembly, and in the stock keeping unit card, you can also add transfer.
So if it’s a purchase item the first one, the fields down here on the purchase will need to be filled in.
I will run through those in another video.
If it’s a production item, you fill in all the fields on the right-hand side for production.
And if it’s an assembly item, you fill in the assembly fields. So basically purchase items is of course item you are buying from a vendor, production item is item you are producing where you have routing and bill of material, and assembly items is like simple production items that you just assembling either to stock or to sales order directly meaning just taking components and maybe some resource time. So it’s a simple way of using production and it’s even more tied into sales order than the production is. If you go to the stock keeping unit, the list of SKUs meaning you can have one SKU per item per location. So if I’m filtering here on item thousand, I can see I have two SKUs; one is for location simple one.
If there’s ask you on a location, the planning will take this SKU card first and not the item card. If there’s not a SKU, it will take information from the item card. So this case if I plan on simple one or warehouse one, it would take one of those SKU. If I plan on simple two or warehouse two or another location, it will take the field from the item card. So basically on the first SKU it says that it’s a production item meaning when I’m requiring replenishing this item on location simple one, I will have to produce it.
Whereas if I go into this SKU card for warehouse one and I scroll down to my replenishment system, I can see this is a transfer item and it takes one week.
Meaning, I replenish it on the location warehouse one by moving it from my location simple one. So this is the way I want the system automatically to calculate how to replenish the warehouse one location for this item.
I’ll run through the fields in another video.