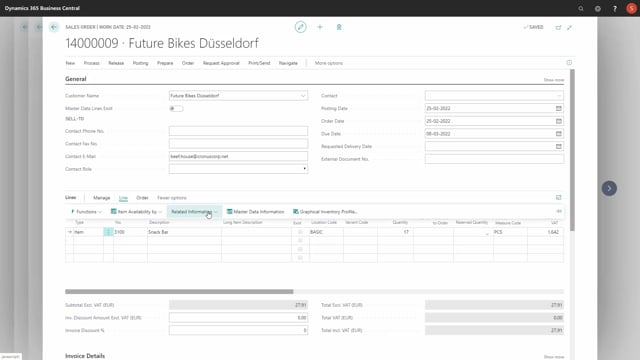
When the overstock item functionality calculates for items that expire, it will take into account items that are actually allocated with item tracking lines.
Let’s show an example here.
If I’m calculating my items that expire and for the example here, item number 3,100 has eight pieces that expires.
And if I look at the graphical profile, I will see here that it’s the end inventory where eight pieces expires on batch number 10, which is the latest expiring batch number.
Whereas if I am changing on my sales order or adding to my sales order, the specific item tracking lines, maybe it’s because I would like to ship a full pallet or full layer or whatever.
So, I’m just entering now one of my sales orders for this item and I’m adding item tracking line for an batch number, which is a late expiring batch number for this item.
So, if we look at the profile now, I can see already in here that I have now an other lot number that expires.
Lot number one will expire, whereas the sales order number, where is it? This one, sales order number nine has assigned lot number 10.
This means if I’m calculating now for expiring items in here, I would expect to have to throw out even more.
In this scenario now, I will throw out 10, which of course also makes sense in my scenario and my end inventory will be minus two.
So, it takes into account everything that is already assigned on item tracking lines.