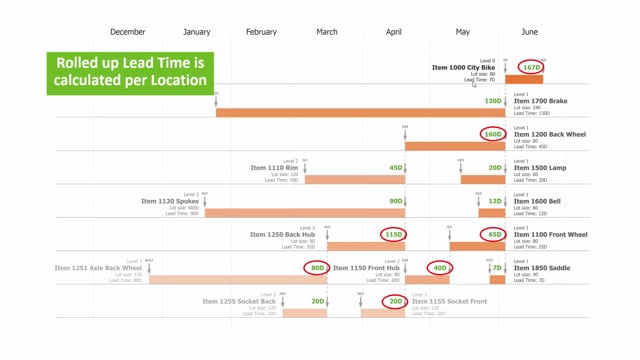
In the Reverse Planning tool, we have a functionality to calculate with lead time or rolled up lead time in here, and we showed how to use it in other videos, and it’s possible to go into the rolled up lead time to see that, for instance, on item 1000 on location code basic, the rolled up lead time is 70 days.
But how is this calculated and what does it do? Let’s look at this in PowerPoint instead.
The function calculate rolled up lead time is calculated like this.
To understand how it calculates up through the hierarchy, we need to start looking down the hierarchy.
So, on level 0, we might have an end date of June 10, which gives us a start date due to the lot size and the lead time on the item.
The lot size on the item card is important because if it’s a manufactured item, a production item, the lead time will be determined by the lot size.
So, on level 1, we have other items that goes into our top level item.
Those items has different lead times, different lot sizes.
Some of them are production items, other are purchase items, but all of them would have some kind of a lead time going here from 7 days till 130 days on the break.
Some of the production item might have other bill of materials, other components on level 2.
When we break down the hierarchy, and again, different lot sizes, different lead times, and if we break down to level 3, etc.
So, this is the structure of the items and we are looking at the lot size fields, which is also the field we use for economical calculation.
Now starting bottom up, we can see that on our item 1251, the lower one, we have 80 days of lead time, and on the socket back, we have 20 days of lead times, and on this third level 3 item, we have 20 days of lead times, meaning that the longest lead time in those hierarchy will be added to the next level.
So, the 80 days on the level 3 goes into level 2, the back hub, and adds to the 35 days on the lead time on the back hub item, plus the 80 days will be a rolled up lead time of 115 days, whereas 20 days here plus 20 days on the production item gives 40 days.
And this way we can calculate up through the hierarchy to find the longest lead time, meaning that the 160 days is coming from 115 days, which is the longest one in level 2, added to the lead time 45 days, and it gives us a total rolled up lead time of 170 days in this example.
So, this is a rolled up lead time, and the reason for having that is if we calculate all our items per rolled up lead time, we need to calculate the top level item at least 170, 167 days ahead to make sure to break down all demands on that item, even though the actual lead time is only seven days.
This is how we calculate rolled up lead time, and we calculate it per location because the lead time could be different per location depending on if it’s a purchase item or a transfer item, etc., and depending on the lot size of the item.