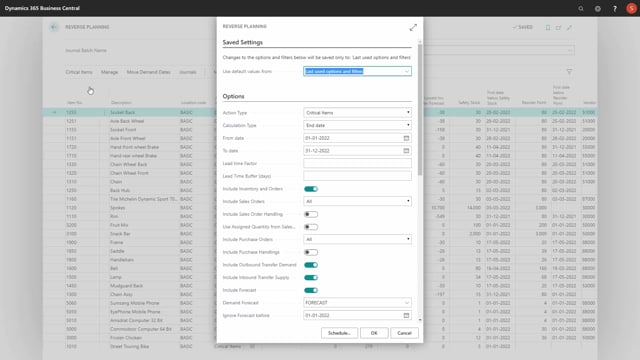
Let’s look at the fields in the request page when you want to calculate critical items in the Reverse Planning.
In the option tab, you have quite a few options to select from, and this creates a lot of flexibility in the way you use the journal.
The action type is coming from the function when you selected critical item, whereas if you selected move order dates, it would have been move order dates, so, it’s the same report that actually runs.
Calculation type determines if you are using end date, meaning a date interval that you defined, or if you’re using lead time or rolled up lead time, which is explained in a detailed video where you only use the starting date, the from date, and then it calculates in the lead time period.
And the lead time factor and buffer days also apply to the lead time calculation types up here.
Include inventory and orders as checkmarks if you want to include, of course, all the orders in inventory.
The reason for not doing that could be if you want to plan for forecast only and see how that works.
Sales orders could be included, all of them only released, or no sales orders.
The next tool field includes sales order handling and user assigned quantity related to other apps.
We’ll go through those and we’ll explain those in detailed videos.
The include purchase order field is like the sales order where you can select between all, only the released, or none.
And you can include, if you want to have transfer orders, both the inbound and outbound side, meaning the demand and supply coming from transfer order on whatever location you are calculating.
You can choose to plan with forecast that will default be set up from the manufacturing setup, or you can select other forecast in here.
And a date for ignoring forecast before whatever date.
Then you can select on production orders, which are supplies, if you want to use planned or released, or a combination of those.
And likewise on the component demands on production orders, you can select, and those are demands.
You can select whether to use firm planned or released, et cetera.
Then you can include planning lines from planning journals, so, if you want to view or calculate including what is already left in the planning journals, so, you want to accept those as being used, you can select this check mark.
And if you use the planning journal, you could also select if it should only be from the start date or with all lines in the planning journal.
And you can select specific worksheets if you want this to apply only to specific worksheets.
Then you can calculate per location.
This check mark makes it possible if you have location filter here in the end, one or more location, it will calculate per location.
So, if you have no location filters, it will run through all locations.
Whereas if you don’t check mark this, it will combine the calculation per location, so, it’s possible to combine all demands and supplies across different locations.
And you can calculate per item variant if you use item variants.
Only use SKU card if the planning parameters should come from the SKU card only.
Normally, if you don’t check mark this, it will take planning parameters from the item card if it don’t find the SKU card.
But if you check mark this, it will only take on SKU cards and if there’s no SKU card, it won’t take any parameters.
You can calculate according to safety stock or zero, meaning if there’s no safety stock, it will use zero.
You can calculate triggering on reorder point or on true zero, meaning not safety stock but actual zero.
And you can use the end inventory trigger if you want the item to be critical only according to the end inventory.
Showing arrows will stop the batch job if an error occurs, otherwise it will just run through.
And then you can automatically suggest quantity to order and you can automatically create orders with those two check marks.
So, if you don’t want to use the different functions of suggesting orders and creating orders, you can check mark this.
And of course you have all the filters on items like everywhere else in Business Central that you can filter on in here.
These are the fields that you can set up in many different combinations.