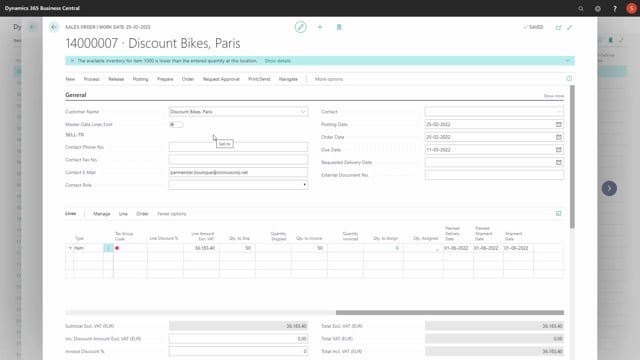
Let me show you how you can use the Reverse Planning to figure out if you can ship a new sales order without making conflicts on other sales orders, if you have all your planning cleaned up.
So, let’s take a scenario here.
First I will look at the graphical profile for my item and see that item 1000 has a positive profile, no zero breaks.
And if I run the Reverse Planning just to show you that my plan is all up to date, meaning if I calculate for critical items within a period and within location code basic, I would expect it to have no actions and if I suggest moving demands, I would expect it to have no actions.
This means my plan is all perfect, everything is good.
Now what happens if we add a sales order in the middle of all those sales orders? I have prepared a sales order line for this item number 1000 in here.
So, for item number 1000 I would like to sell 50 pieces and if I’m scrolling right I can see here that I’ve added a date, the 1st of June.
So, is it possible to ship this sales order without creating too much noise on other sales orders? If I look at the graphical profile now, I will expect the inventory to be somewhat zero.
So, I have a lag of 38 pieces and it will make noise on other sales orders.
If I enter the Reverse Planning, first what I would like to do is to calculate for critical items, finding critical items and I would expect at least this sales order to be critical, looking only for in inventory and on location code basic.
This will provide at least this one line and I could suggest quantities to order and if I use order modifiers it will in this scenario make 40 because I have some order modifiers and I will move this into my quick journal.
So, I will create orders and it moves the order into the quick journal.
I have now one line.
Then I will calculate my critical items again because I would expect this one line to create depending demands.
So, this way I have to break down my hierarchy and calculate as many times as it takes to have calculated for all lines in here.
Just like this.
And I think the layers that I have here is about two or three layers.
So, I’ll have to calculate sometimes.
Let’s do this quickly and break down the complete hierarchy.
So, right now I’m just suggesting quantity, adding all the items that I need to do to fulfill all my demands for this new order.
And I think we should soon be there.
I’ll expect maybe one line more or one low level code more.
Now I’m done and if I open my quick journal in here I can see that it would suggest five new order lines that I need to make to fulfill this demand.
Now when I calculate move demand dates, and I’m of course not triggering an inventory for that one, I’ll have to try to find the consequences of what we’re doing here.
So, first of all, in the journal I should have added the possible dates in the quick journal to figure out what was possible.
So, I could have opened my quick journal and looked at the line, maybe talked to the vendors in here and said what is possible for those items.
And then when I calculate the move demand dates I can see here the suggestions of what to do.
And as I can see here, one of the consequences is that we need to handle item number 1010 and likewise item number 1000.
And if I scroll right I can see here that for instance the item number 1900 now needs to be moved from 6th of June till 20th of July.
And it has consequences on the same production order down here.
So, we need to move a production order due to that.
And now I can investigate those lines looking into the item number 1900 with my graphical profile, seeing what is happening here.
And I can see here the planning line causes a negative inventory, therefore it moves one of the production order lines here.
I think it will move this item 169 and it moves it until the 17th of July plus my move order date, which is three days on the item card.
And thereby it calculates up through the hierarchy.
So, the consequences for adding a sales order line of 50 pieces on the 1st of June will be that I have to, first of all, to move the same sales order until June 18 if it should be possible.
And second, that I will have to move another sales order.
So, I have to contact this customer to figure out if this is possible or to prioritize otherwise.