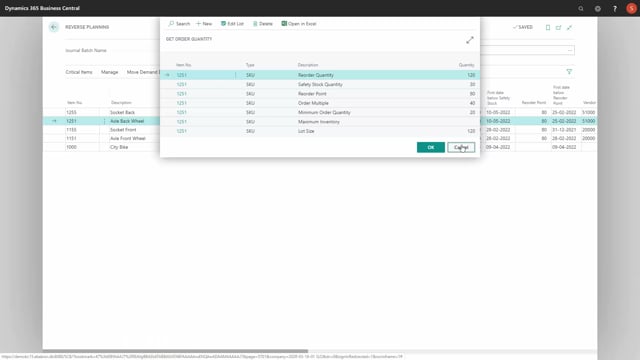
After calculating critical items in the Reverse Planning journal, it’s possible to fill in the quantity to order from a small function called suggest quantity to order.
And even though it’s only small for a field, it’s rather confusing to understand.
First of all, let’s look at the inventory profile for an item.
So, this item has an inventory of 68, an inventory of minus 55, including forecast, the lowest inventory of minus 44, safety stock 4, and maybe even some other parameters, order multiple, lot size, and safety stock quantity set up on a SKU card.
If we look at the graphical profile for such an item, how would we actually like to suggest orders? Would we like to suggest from the minimum actual expected amount, or the minimum forecasted amount, or the end inventory, and to zero, or safety stock, or reorder quantity? so, to figure out the size of the order we need to plan, we can do different things.
Going into the suggest quantity to order, the first option would be to calculate from zero, and calculate to, for instance, safety stock, like this.
This is a rather stupid example, just to show you that in the last scenario, from zero till safety stock is 5, nobody would use that scenario.
But it would make sense if you used the scenario from zero till, for instance, reorder quantity, because that would mean that you could lay out orders only in the actual reorder quantity.
So, this would be clean numbers that we know that you can use.
You could also suggest calculating from the end inventory, and that’s probably the most common thing to do, to use the end inventory quantity, and then calculate up till either safety stock, or reorder point, or even reorder quantity.
So, if we calculate from end inventory till safety stock, this would mean 68 on this line, from end inventory minus 38, till safety stock 30.
Likewise, on the last one, from end inventory 55, up till safety stock 5.
We could also have selected to calculate from the lowest inventory, or even the lowest inventory including forecast, if we wanted to, so, the lowest inventory in the period, if we don’t want to move the orders in here, that would be, in this example, 49, coming from lowest inventory of minus 44, up till safety stock, etc.
Let’s look at the two modifiers over here.
If we calculate, the most common one would be from end inventory to either safety stock or reorder point, in my belief.
And this would look like this.
68 and 60 on the last line.
If we suggest orders using order modifiers, it will take into account the order modifiers on the item card, or the SKU card.
So, now, instead of 68, on the second line we have 80, which is because we have an order multiple of 40, so, this is one of the order modifiers.
Likewise, on the 90, we have an order multiple of 45.
But be aware, this order multiple is coming from the item card, meaning there’s no SKU card on this item, on the location basic, whereas the other one had actually a SKU card, so, this is entered on the SKU card.
You could select the last option, only use SKU cards, meaning only take the quantities from the SKU card into account, so, if there’s no SKU card, don’t use it.
So, in this scenario now, it says 38, because there was no SKU card, I saw that by looking up here, and it looked into the item card.
So, the end inventory is 38, and it calculates up to zero, because we have defined no safety stack, no order multiple, no nothing, because there’s no SKU card.
So, the point of using this checkmark, of only using SKU card, is to avoid getting too much items.
For instance, if you have locations in cars with technicians driving around with many different locations, you might only want to exactly fill up to zero, and therefore you don’t define any SKU cards, and then it won’t take the information from the item card, otherwise you could fill up on all the cars too much.
So, there’s a lot of flexibility in the function to suggest quantity to order.