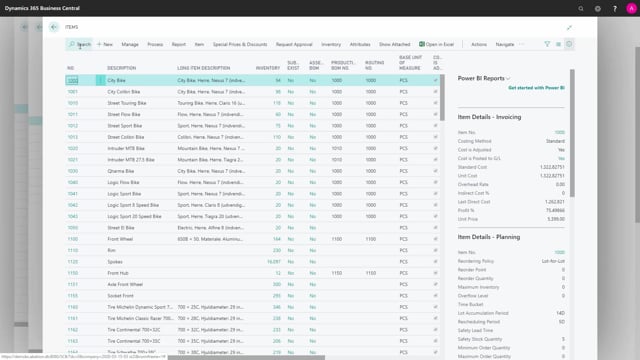
Normally, if I’m on the planning worksheet using the MRP plan, my data needs to be set up correctly. And the MRP planning is very cool when all your setup is correct and you maintain all your data correctly, etc. But if you don’t maintain your data or you do it wrong, the MRP plan is not working very nice.
So you’d be have to be aware of that. In this scenario, I’m planning on low level code one, just to show you on whatever filters here, and it calculates all my item in low level code one. This is a very typical error that we see with our customers that are trying to use MRP planning.
As you can see, I have all my items, but my item 1900 is not in here. Whereas if I have run the reverse planning worksheet on the same filters, calculating for critical items, looking at low level code one, and I’m calculating here, my first item 1900 is actually popping up. And it has a negative end inventory, negative inventory as we go along. So this is of course a critical item. Now, why didn’t it pop up in my MRP planning? That I would have expected to do. And of course, because the data is not set up correctly, I’ve just moved the reordering policy on the item.
So if you look into the item card, the reordering policy is not filled in, which is a typical mistake when making new items or not maintaining items correctly. This is just one simple example. You need to set up reordering policy correct and all your reordering parameters. So with the Reverse Planning, it’s working out of the box because it’s just showing you simply the inventory, the inventory levels, and it tells you, you need to do something.