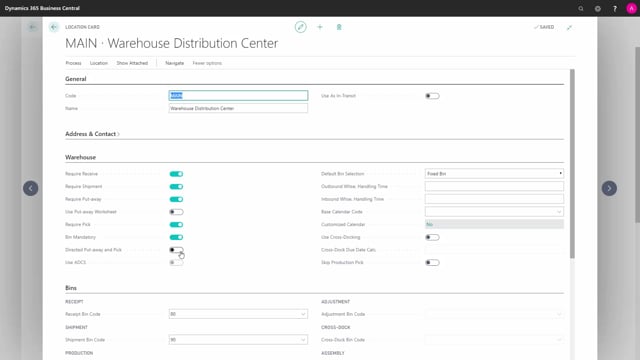
How do the warehouse processes depend on the configuration of locations?
In Business Central, the location card determines how the warehouse setup is working. Let’s see the different possibilities on the location card related to the inbound side.
This is what happens in the video
First, let’s look at the very basic setup. We have a purchase order. We can receive the goods, and we put it on stock. We have no warehouse activities whatsoever. That will in Business Central look like this.
If we enter the location list in Business Central, and I’ve made a basic location and there’s no checkmarks at all in the warehouse tabs, which means we don’t use bins, we don’t use any warehouse documents at all.
Let’s look at another location card as an example in here. We could take the external location that I’ve created, in the external location I have check-marked require receive and require shipment, but none of the other ones and that will look like the following in a PowerPoint view.
We have a purchase receipt, and on the outbound side, maybe a sales shipment, and on the purchase receipt, it’s possible to combine purchase orders to receive goods, and it’s also possible to make purchase receipts but the user cannot see prices because the receipt only contains quantities.
Next scenario on a location could be a scenario like this, with no purchase receipt and no sales shipment, but with all the main functionality, and we have a put-away on the inbound side in Business Central, in this scenario It will be called an inventory put-way because we have no purchase receipt, so we use an inventory put-away directly, and we use the bins. But we put away directly on the inventory put-away made from the purchase order.
In Business Central this scenario will look like this: I have my distribute location and I’ve checked mark the require put-away checkmark, and the bin mandatory, but not the require receive checkmark. So I’m making inventory put-away document and post directly on that document related to the purchase order.
We could also make a location like this bin simple location, only with a checkmark in bin mandatory, meaning we don’t want to use any warehouse documents but receive directly on the purchase order, and handle inventory movements, or inventory actions directly; that will look like this in PowerPoint.
In this scenario, we have a purchase order we received directly on the purchase order into the bin code on the purchase order line, and of course, we have internal warehouse activities as well, which all relates to the simple bin handling functionality.
The last scenario will be something like this, we call it advanced.
So, the first one is what people typically will call basic with no checkmarks. All the other examples will be what we call Simple Handling, and the advanced one will be something relating to this picture, where they have all the warehouse documents from the purchase order, we created at purchase receipt and from that we create a repost, and after posting it creates a put-away and we can put the goods into inventory.
That could be made of two scenarios on the location set up. Let’s look at those.
The first one will be the warehouse management center location, where I have added the full check mark, we call it the directed put-away and pick checkmark, which will automatically force a checkmark in all the other warehouse documents. Meaning it has to use all documents.
This functionality has a lot of extra features related to it, but from a document perspective, this will be the same as my main location where I manually checkmark everything but not the directed put-away. So in this scenario, I have less functionality, but the documents I use will be the same.
So this is a different way that you handle the warehouse management setup on your location card. And of course in the same database on different locations in the same company, you can use different locations but different setup.