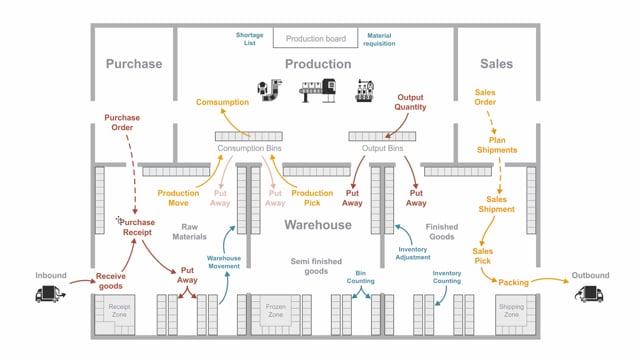
How does warehouse processes work in Business Central?
When we talk about warehouse, we mean both the inventory level and the warehouse level with all its complexity and functionality. Let’s go through it all in this video.
This is what happens in the video
Let us run through a short overview of warehouse processes in Business Central.
So when we talk about warehouse, we mean both the inventory level and the warehouse level with all its complexity and functionality.
Let’s run through those shortly.
First of all, we have the order documents which is the purchase order and the sales order and those are the documents that we confirm with our vendors and customers.
Second, we will have purchase receipt and sales shipment.
Those are documents where we can bundle several purchase orders we expect to receive.
Maybe several purchase order lines from different orders on the same vendor or even from different vendors in a container in one receipt.
Likewise on the sales order.
We could have a sales shipment why we bundle several different sales orders into one shipment, maybe ship it to an external warehouse or handle it ourselves in the inventory, and the next step will be to be able to create put aways from the purchase order meaning once we receive the item on the purchase receipt, we would like to store it into a bin in the warehouse, a specific bins.
We use the put away for that.
On the sales pick, we would like to be guided through a routing in the inventory to pick the goods for the customer and then to pack it and ship it.
But we’d also do pick for production, for instance, or for assembly orders, for transfer orders so those are all the same type of documents and as a warehouse employee, the pick will look the same.
So our pick will just be a pick activity, which is actually the movement in my warehouse.
We could also do a moving document instead of a pick document and the difference will be that if we create a pick for specific document, production or consumption here, the pick will be allocated for that order and we could post it directly as a consumption afterwards on the production order.
Whereas move is just an activity as a signal for the inventory to create a movement to move the items into the consumption bins in the production area.
When the items are done being produced or assembled, we could output the quantity to an output bin in the production area and then create a put away from the output bins back into the warehouse.
And the put away is the same type of documents as from the purchase receipt.
So as a warehouse employee, I don’t care if the item is coming from a vendor or from production or from a transfer order or even a sales return order, I will put it away and get suggested some bins to put the item into.
A put away could also be made from the consumption bins with remaining quantities meaning I have produced material and they will be consumption items lift that we didn’t use in the production and the warehouse people will need to put it away with movement or put away in the warehouse.
A warehouse movement is an activity in the warehouse to move items from one bin to another, and it could be done through a document which will be planned movement that somebody tells me what to move or it could be like a impulsive movement in the warehouse where I just take some items from one place and put it on another place.
We could do inventory adjustments meaning if the bin we count with a specific item seems to be wrong, we could do an adjustment just in the warehouse area and later synchronize it into the item level.
We could do counting per bin or counting per item or counting per section in the inventory.
So it’s possible to, of course, count the inventory from a warehouse entry perspective.
So this is all the functionality in the warehouse management in Business Central.