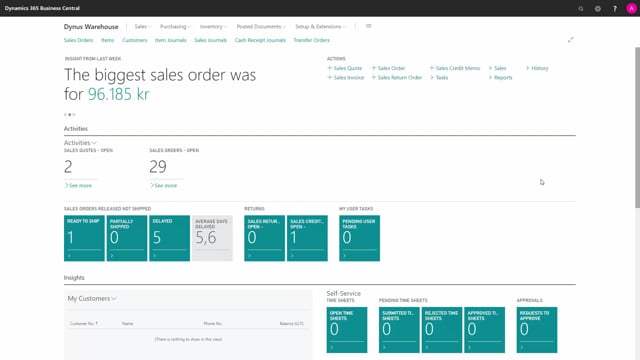
How do you do structured inventory counting?
In Business Central, you can use physical inventory orders for more structured counting on your inventory, and those don’t apply to location with the directed put away and pick checkmark. So, it’s only for what we call simple location and advanced location without that checkmark. Let’s just take a look at how it works.
This is what happens in the video
I can enter a physical inventory order list to create a new order. I would like to calculate on main, for example, and then I could calculate lines just per item.
I’ve added here an item filter and you can calculate on different filters. We will show that in other videos.
In this scenario, I would just count per item and I will count those different items on different bins so it splits the lines if the item is on different bins.
From here, I need to create recordings and the recordings is the document I will print, and that I will use for my warehouse people to do the counting.
I could print the physical inventory order from in here just to see what the complete inventory should look like and it displays also a serial and lot number information for the items, but this is not a list meant for the actual counting.
So, I will do recordings to make the counting and I can see that I have item with item tracking lines so maybe I want to add two recordings: one for the item tracking which is maybe more manual or complex, and one for the rest of the item.
This means I could create the recording.
I could filter on all the fields on the physical inventory order lines, for instance, the use item tracking field.
And I will select okay, so now it has made for me a recording which is the document I want to print.
So, this is the physical inventory recording list and from this recording, I could print the document and I can see the two items here with the item tracking.
I could print this document, hand it to some warehouse employee, and make them go and count the items and write down all the serial number information or lot number information.
And likewise, I could do a physical recording on the remaining items.
I could just make a new recording without any filters like this, and select only lines not in recordings, meaning it will just take the remaining lines that have not already made whatever recordings on.
So, in this scenario, you can create recordings per bin, per shelf, per whatever so it’s easier for you to create many different recordings that you can hand out four different warehouse employees.
So, if I’m just showing you the last recording I made, now we have two recordings here, and again, I could print this one, hand it to some warehouse employee.
They could go around the inventory and do the counting, enter the actual quantity and then enter back in the recording.
We will show you in a video on the physical recording how to do the actual registrations.