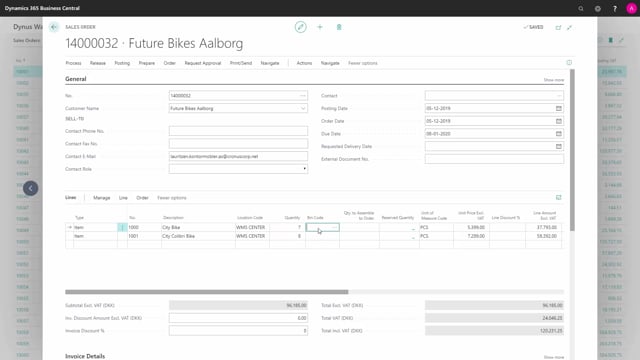
How is the Outbound Warehouse flow with Directed Put-away and Picks required?
I will show you a run-through in Business Central of a complete outbound flow with the location that uses the directed put away and pick checkmark on the location card.
This is what happens in the video
This means I will create a sales order and from the sales order after releasing it, creating a warehouse shipment, then I will add other sales orders to the warehouse shipment then create a warehouse pick and from the pick, I will change some of the bins while running around my inventory and I will split some of the lines to pick from several different bins then I will register the pick, post the shipment and thereby post the several sales orders on the shipment.
Let’s see how it works in Business Central.
First, we will look into the location that I’m going to use as an example.
And that’s my WMS center, which has the checkmark directed put away and pick meaning that all the other checkmarks will be default set and not able to change.
Now, I’ll make a new sales order for one of my customers and I will add the item numbers that I’m going to ship or sell in whatever quantities.
One of the differences between having the pick checkmark or just selecting the different selections on the location card is on my main location that has all the different checkmarks but not the directed put away check.
It will display the bin code and it’s possible to change the bin code and look up whereas when I have the pick checkmark, it will say only that shipment is required and you cannot see or change the bin code on the sales order line.
So that’s a small difference of those two functionalities.
I release the sales orders.
I will create a warehouse shipment and it opens automatically because I’m creating it from the sales order in the scenario.
On the warehouse shipment, I could add more sales order documents or other types of documents to my shipment.
So I’m going to pick for several customers and maybe you saw that it was different customers as well.
And I can create a warehouse pick and be aware that the status is open on the shipment and it releases automatically when I create a warehouse pick.
So you can see now it’s released and I can navigate into the warehouse pick.
Here we are.
These are all my pick lines.
I might want to change some of the bin codes to select another bin, for instance, like this.
I could change it directly here on the pick and I could print the pick to see what it looks like.
So either I would have a terminal scanner or a scanner device to run around in my warehouse, otherwise, I would just print this document and then add quantity to handle.
So one of the differences with using the pick checkmark or not is the default filling in the quantity to handle.
So with the directed put away and pick, I would like everything to be very controlled.
So I’d like the warehouse employees to actually enter physically the quantity to handle on the printed pick.
Let’s go back in Business Central.
After performing the pick, I need to fill in the quantity to handle on each line to be sure to tell the system that I’m doing correctly.
If I’m actually handling, in this scenario, maybe only two because I took some of them from one bin and the other two from another bin.
It’s possible to split the line.
It will create a new line where I can enter the other bin that I’m taking from like this.
And I can fill in further on quantity to handle on all the other lines.
I need to fill this in manually and the point of having the pick checkmark on my location or the directed put away and pick checkmark would be that I would like my warehouse employees to confirm all the activities they’re doing.
Now, it’s possible to register the pick like this, and back on my warehouse shipment, everything is picked so I can now post the document, post the shipment, and thereby also post the three sales orders that are attached to this shipment like this.
You can see it as posted, three sales orders.
Both the sales orders I was working on here and the two others that I’ve fetched from my warehouse shipment.
So the ship quantity is now 7 and 8 on this sales order.
So this is the full flow of the complete warehouse functionality and the only thing that you didn’t see here was how to use the functionality to create the shipment more intelligent like with a pull strategy and create the picks with a pull strategy.
We will choose that in other videos.