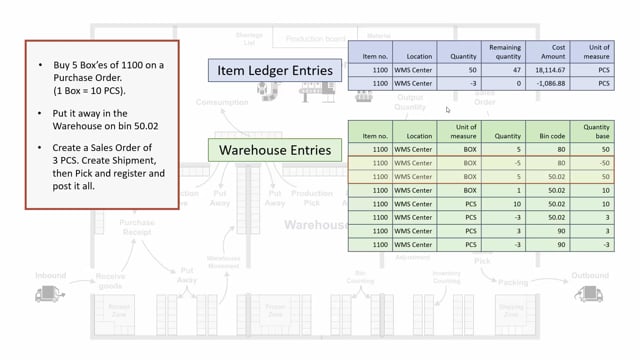
How does Item Ledger Entries, Warehouse Entries and Bin Content work?
Working with inventory and warehouse in Business Central, we basically create two interesting kinds of entries: the item ledger entries and the warehouse entries, but we also have the bin constant table that is some mixture of the warehouse entry and I’m going to show you how this works.
This is what happens in the video
Normally, the item ledger entry applies to documents and to handlings outbound / inbound in the house and the warehouse entry relates to things that happens in the warehouse and the correlation between those is very important to understand.
Let’s take a look at those entries in Business Central.
From my item 1100, I can drill into my item ledger entry and view the item ledger entry in here.
I can see that I have bought 50 pieces and I have sold three pieces.
Likewise, if I’m looking at my warehouse entries for this item, I can see there is quite many entries and they all have quantities and different unit of measure.
It could be different units of measures but for only two items ledger entries in this scenario, I had many warehouse entries.
And the last thing would be the bin content.
And if we look at the bin contents and I would just filter on the location that I’m looking at.
I can see here that we have four bin contents.
They reflect quantities and units of measures.
So whereas the item ledger entries hold only unit of measure code, it also holds prices, sales, and cost prices, but the warehouse entries and the sum-up of warehouse entries and bin contents only holds unit of measures and quantities.
Let’s look at this in Powerpoint.
The entries we saw in Business Central had followed this scenario.
We have bought five boxes of this item.
One box equals 10 pieces that is set up on the item card, and we’ve bought it on a purchase order.
This means that we make an item ledger entry of 50 pieces that we add to the inventory.
Originally, the remaining quantity would have been 50 pieces.
Then we put it away in the warehouse on a bin.
It doesn’t do anything to the item item ledger entries then we create a sales order, a shipment, and pick and register and post all of it and it creates one item ledger entry of -3 pieces.
So the item ledger entries would always be in base unit of measure.
The quantities will always be in base unit of measure, and you can see the remaining quantity is maintained on the old item that changes.
So an item ledger entries can be modified again and again.
The warehouse entries reflect everything that happens in the warehouse and once the entry is created, it will not be maintained.
It doesn’t contain any prices, only quantities, unit of measures, and bin codes that is the core of the warehouse entries.
So with the warehouse entry, we want to tell where the item is in the inventory on which bins.
Let’s run through this scenario here.
First of all, we have bought five pieces on the purchase order, sorry 50 pieces but five boxes and it comes into the bin code 80 which is our receive bin, but in the warehouse entry, it uses the unit of measure code with five boxes, where’s the item ledger entry will be 50 pieces.
Secondly, when we make a put away, we take out the five boxes again, and we added to bin code 50.
02 again in boxes.
The next thing that happened will be the sales order pick.
While creating the pick, it will automatically suggest five or four lines in this scenario because it needs to break up one box on bin code 50.
02 and put it back on the same bin code in pieces.
So it makes a suggestion for a break because I need to pick three pieces and that’s what happens afterwards on the pick, I’m taking three from the bin code adding it to the shipping bin.
And last of all, I will sell the three for the customer and that takes out three, of course.
So this will be my warehouse entry flow.
If I’m looking at the bin content in this scenario, I can see it will be a sum-up of the warehouse entry.
So from the item card when you look at the bin content, it displays how many quantities do you have in which unit of measure on your inventory.
So in my scenario here, I will end up with four boxes and seven pieces.