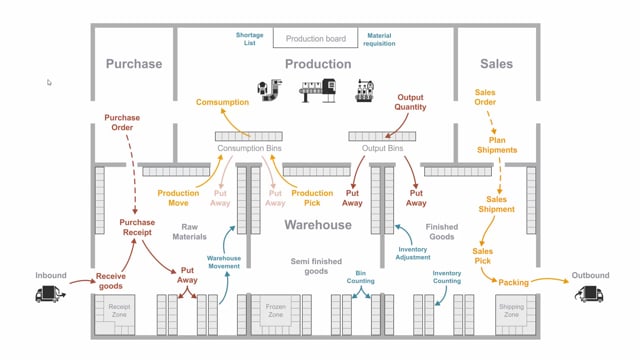
How does warehouse processes work for production and assembly?
If you’re using assembly order or production order you want to create and you use warehouse the same time you want to have pick and put away activities for your production documents. So from the warehouse perspective, we need to create a production pick or a sample pick to take the item in the warehouse.
This is what happens in the video
Go a picking route to find the item and then to place them in the consumption bins in the production environment.
So a pick activity is an activity where we take specific items, make a movement, and allocate those items to a specific production order or assembly order.
From a production order or assembly order, you could also create movement activity.
This is not a pick.
This is just moving documents which makes it possible to take the item and move it into the consumption bin.
And the difference between those two document types would be then in the consumption bin, the item will be expected either for a specific document in the pick scenario or they will just be filled into the consumption bin.
So if you just hailing items in inventory and then moving in again and again and again, you should maybe use moving documents.
Both activities will create warehouse entries where you move items from one bin to another bin.
This means now the item is not in the warehouse area, but in the consumption bin area in the production.
Next thing would be that the production people will consume the item for either the production or assembly order when they actually use the item that could be done in several times and each time it creates item ledger entry with the consumption quantities.
After consuming the items to production, they might want to return some of the consumption items if the consumption bins are not empty that the warehouse people moved in a full pallet of goods because it was easier and after producing the item in the production area, they will ask the warehouse people to move the pallet back on inventory.
This means they could create some kind of put away document to tell the warehouse people to put the item back in inventory or the warehouse people could just make a manual ad-hoc movement on the items back into the warehouse.
When we post the put aways on the movement, we will create other warehouse entries, of course, that maintain the warehouse quantities of the item in the correct bins.
Next step will be for the production people to output the finished quantity and they will typically put it into a production bin or an output bin to tell the warehouse people that this is ready to be put back into the warehouse.
So when the output is posted, it will create item ledger entries and now the quantities will be available in the item card and on stock.
The warehouse people will need to perform a put away to get the item back– the new item into the inventory as a semi-finished product or a finished product and put them into specific bins into the warehouse, which of course creates warehouse entries.
So these are only processes related to production or assembly using warehouse management functionality.