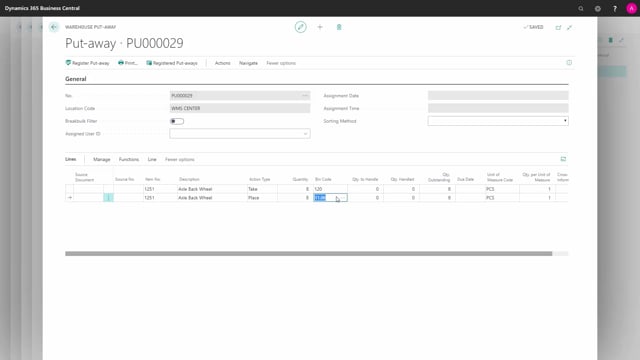
How do you return components to inventory with different location setups?
Working with warehouse management and production at the same time, you might have a situation where you have posted consumptions on production orders and you have remaining component items that need to go back on inventory because you consumed less than expected or you moved into the production more than expected and depending on your location set up, this could be done in different ways.
This is what happens in the video
Let’s look at some of these scenarios here just to see the advantages using one or the other.
On my item 1251 if I look at the bin content on the item card, I can see that on location Main on bin 120 which is my production bin, I have 12 left and on location WMS Center, I have eight less left.
This is the directed put away and pick location. And I want to move those back into my bin 11.06 on both scenarios, which is my main bin. Let’s see how it could work.
First of all, on the main location which is not directed put away and pick, I need to create an internal movement to be able from that to create a movement to move it back into inventory.
This is of course only if I’m not using the item reclassification journal directly with one or the other bin code.
So if I want to create a document, I will create a new internal movement that I have prepared here entering my two bin numbers and my location code, the item number, and I need to enter also where do I want to pick it from so I’m adding both the from bin and to bin and, of course, the quantity.
From here, I can create my inventory movement, which is now created like this. I will just try to find it and open it.
So this is now a document I can use for my warehouse people to take 12 from one bin code and add 12 to the other bin code and then register the movement that does the posting here on my location Main which is an advanced location without the directed put away and pick.
If I want to do the same scenario on my WMS location, which is using directed put away and pick, I could do two scenarios: one would be that I could make a movement manually.
I need to do that from a movement worksheet and I have prepared a line in here on the item number and I will enter the from bin number, but if I don’t know where to put it, I don’t have an idea where to add it, I will just enter the quantity here and then create my movement directly from here and then the warehouse people will figure out where to set it.
And this is one of the advantages of using the internal pick that I’m showing you right away. Let’s first look at the movement that we have created.
This is now a warehouse movement because it’s an advanced location with directed put away and pick.
If I look at this movement now, it has made a take action and a place action and I need to somehow tell the system where to place it when I’m registering this movement.
Let’s just delete it and look at the last scenario which could be the internal put away which only applies to warehouse with directed put away and pick.
The advantages of using this one could be that I’m saying where to take the item only creating a line with the quantity and no bins and then let the system do the rest by creating the put away like this and I will open the put away which is now a warehouse put away and it’s a document for my warehouse people.
And when I look at this put away, I can see that it had to create both a take line and a place line, but it also suggested more or less intelligently where to put it based on my setup on my bin content table and where the item already is.
So, in this scenario, I can do more logic stuff automatically by figuring out where to put it and I would just register this put away like a normal warehouse activity.