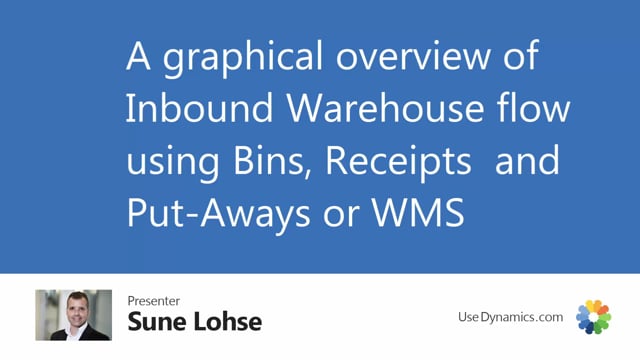
How does warehouse management work with bins, receipts and put-aways or WMS?
Let’s look at the full warehouse inbound flow if you use either directed put-away and pick, meaning the big checkmark in the warehouse in the location set up, or if you use both require receipt, require put-aways, and require bins.
This is what happens in the video
So, if you use all of the possible documents, how would it look in Business Central?
First of all, you have a purchase order or maybe several purchase orders if you want to bundle them. And the first thing to do is to release the purchase order. This will create a warehouse request automatically per purchase order.
Next step will be to create a warehouse receipt. This could be done either from each purchase order creating separate receipts or from the warehouse receipt by fetching the purchase order and bundling them into the receipt.
Now the warehouse receipt is the document where we actually do the receipt; you can print it out and give it to the people in the warehouse zone. And they will enter the quantity when they receive the goods, and when they post the receipt, the item will actually go from not existing in Business Central and going into the receipt zone, meaning it will post a posted purchase receipt, which creates item ledger entries, and it will post a posted warehouse receipt, which creates warehouse entries. And it will also create a warehouse put-away, whether it’s a document prepared for taking the goods from the receipt bin and adding it into the inventory bins where you want to store it.
So the next step would be from the warehouse put-away document to print out the document, perform the actual put away and register which bin you are adding the item to and in which quantities, then you register the put away document or modify the lines if you used other bins, and this will create a registered warehouse put-away document while moving the items from the receipt bin into the warehouse bins, and it will also of course create warehouse entries to handle that.
So this is the full inbound warehouse flow.